Nízkotlaké lití do forem
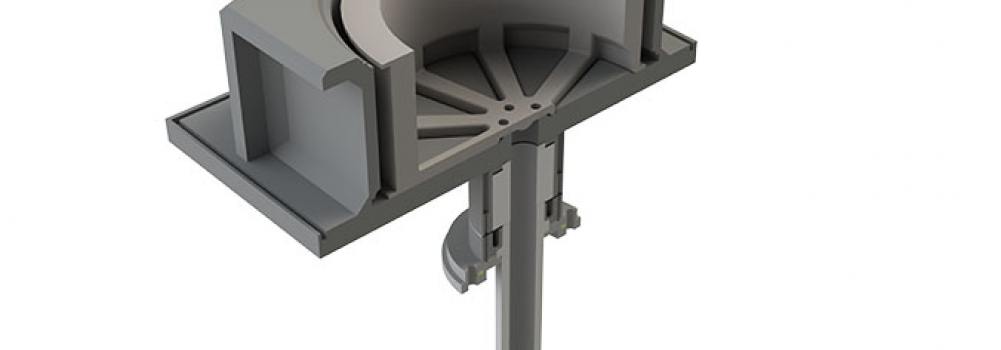
Nízkotlaké lití do forem (LPDC) je postup, který je běžně používán v dnešních slévárnách a při kterém je forma pomalu plněna roztaveným kovem, čímž jsou omezovány nepříznivé vlivy víření. Výrobky, které jsou určeny pro automobilový průmysl, zahrnují lité ráfky kol a rovněž součásti systémů zavěšení kol, řízení a motorů. Díly, které nejsou určeny pro automobilový průmysl a které jsou běžně vyráběny za použití technologie LPDC, zahrnují potrubní oblouky a zvonové uzávěry. Postup LPDC umožňuje získávání odlitků s velmi dobrou metalurgickou kvalitou. Výhody postupu LPDC zahrnují:
- dosažitelnost vysoké míry výtěžnosti (zpravidla přes 90 %);
- snížení nákladů na obrábění dosahované díky skutečnosti, že nejsou potřebné vtokové kanály;
- vynikající míru kontroly nad procesními parametry, které je dosahováno díky vysokému stupni automatizace;
- dobrou kvalitu zpracovávaného kovu, které je dosahováno pomalým plněním bez víření a řízením dynamiky tuhnutí a která umožňuje získávání příznivých mechanických a metalurgických vlastností odlitků, včetně nízké poréznosti.
Kritické problémy, které musí provozovatelé nízkotlakých licích linek řešit, zahrnují čistotu kovu, obsah vodíku, licí teplotu, nastavení časového průběhu cyklu odlévání a povrchovou úpravu a údržbu forem.
Slévárenský tým společnosti Pyrotek se zaměřuje na zlepšování kvality kovu a dosahování vyšší produktivity při tlakovém lití prostřednictvím integrovaných systémů, které jsou určeny pro tavení, předávání, úpravu, udržování a odlévání kovu. Řešení určená pro proces LPDC zahrnují přepravní pánve, kelímky, plochá i kruhová těsnění, radiační topná tělesa, termočlánky, nálitkové kanály, žárovzdorné vyzdívky a další položky.
- Zlepšená kvalita kovu
- Snížené množství kovového odpadu
- Zvýšená efektivitu procesů