Metal Casting System
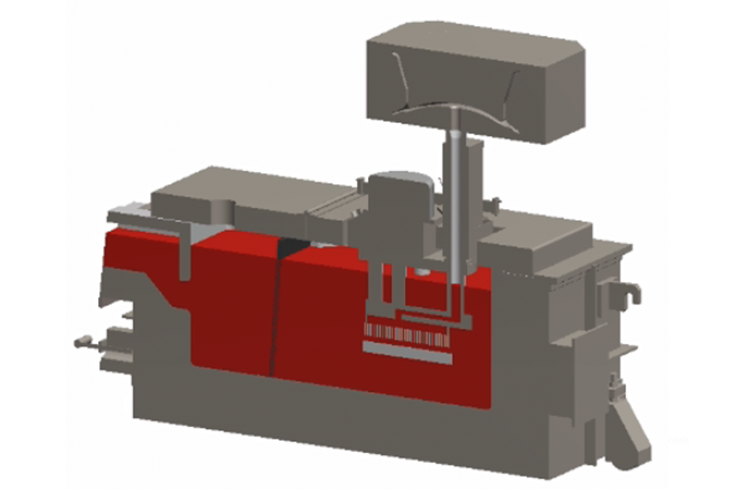
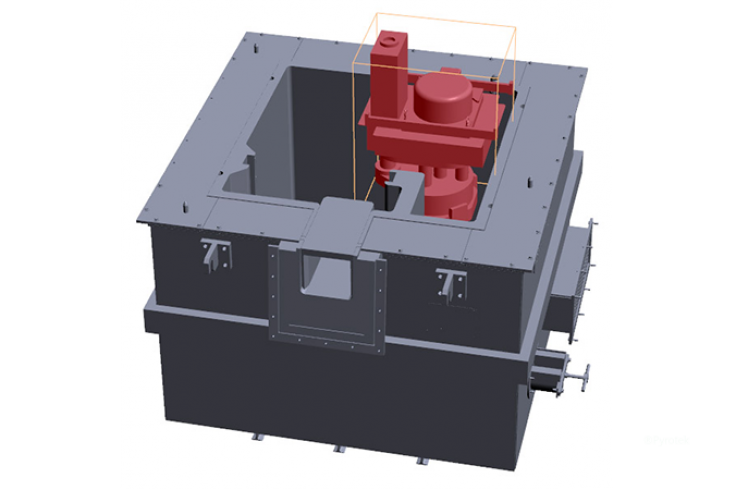
Overview
Pyrotek's metal casting system (MCS) is an innovative casting technology that offers a new alternative to traditional casting methods. The MCS moves molten metal between the holding furnace and mould using a precision casting pump. The MCS achieves volumetric and non-turbulent filtered metal feeding by having full control of the pump's flow performance.
The precision casting pump eliminates the need for costly compressed air, increases capacity and productivity, and significantly reduces turbulence during casting cycles. The MCS has the capacity for more than one pump in a shared furnace.
The MCS furnace has an immersion heating system, allowing it to stabilize bath temperatures and prevent stratification often created in top-heated furnaces. The MCS furnace provides a potential energy consumption reduction of 30–40 percent compared to radiant heated systems. The furnace is not pressurized and can be filled any time during the casting cycle, reducing downtime for refilling. Its airlock design keeps air out and allows for the use of an inert cover gas, or "nitrogen blanket," that prevents oxide formation and hydrogen absorption.
Precision casting pump benefits
- Precise flow and pressure control during mould filling
- Maintain and transfer metal at a uniform casting temperature
- Hold a static column of metal close to the mould
- Accurate and consistent metal transfer and dosing
- Multiple casting pumps in one furnace
- Reduces casting scrap rates
- High accuracy and repeatability of metal transfer/dosing
Immersion-heated furnace benefits
- Maximize metal quality with applied filter techniques
- Reduce maintenance frequency and enable easy component replacement
- Reduce dross formation in holding and casting furnaces
- Non-pressurized furnace can be filled any time during casting cycle
- Optional airlock feeding system
- Less downtime refilling the furnace
- No temperature stratificationÂ
Pyrotek Offerings
The MCS and precision casting pump are proven alternatives to transfer filtered metal in a controlled and non-turbulent way into the casting mould in low-pressure casting, high-pressure die casting, gravity casting and dosing applications.
- Provides energy efficient holding furnace
- Reduces dross and improves metal quality
- Precise flow control and low turbulence
- Shorter production cycle times
- Increases capacity with lower scrap rates