Furnace Refractory
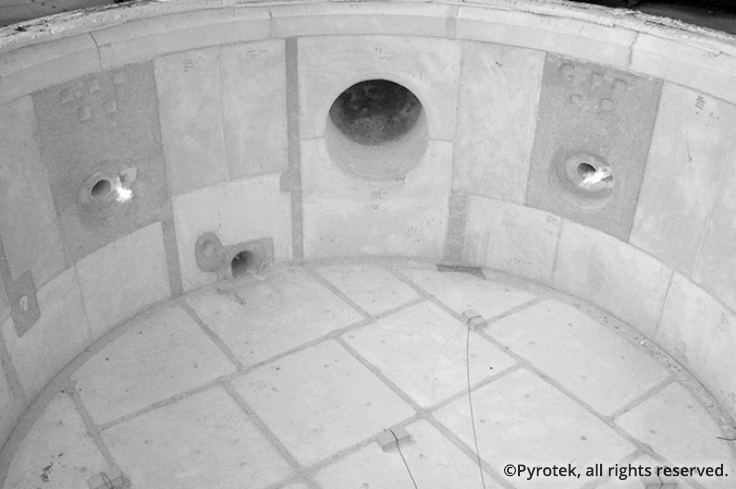
Overview
Furnace refractory is the ceramic component of the furnace that directly interfaces with the contained molten aluminium, also referred to as the working liner. The term "furnace refractory" may refer to either the working liner of a holding furnace or melting furnace. Additionally, furnace refractory is typically referred to in relation to its location in the furnace: lower walls, belly band, upper walls, roof, hearth, subhearth, door surrounds (jambs, sills and lintels), ramp, inlet, outlet (tapout block) and charge well.
Furnace refractory plays a major role in furnace efficiency, furnace maintenance costs, life of a furnace shell and more.
Pyrotek Offerings
Pyrotek’s TAB Refractory Services is a world leader in the aluminium industry, providing the best quality furnace linings and refractory services, with more than 50 years of experience and knowledge. Since 1974, TAB has provided solutions for customers around the world in more than 30 countries. Work is done on both melting and holding furnace designs of all kinds: reverberatory, round top loading, static, tilting, rotary, tower, and die casting.
TAB’s technical engineering department, with experience and advanced training, assist customers by providing custom solutions and designing bespoke furnace linings to extend the service lifetime and improve the performance of furnaces. TAB provides complete turnkey refractory services from design and engineering to dry out and commissioning. TAB also has decades of experience in furnace lining maintainance, to further maximize service life of furnaces.
TAB has a long history with global customers, providing the lowest TCO (Total Cost of Ownership) furnace linings, due to the quality of the initial reline and the maintenance service provided throughout the lifetime of the furnace.
Pyrotek's years of experience casting refractories have resulted in a selection of the best refractories from many suppliers in addition to experience in quick, high-quality installation of brick liners, monolithic/cast-in-situ liners, and/or big block liners.
- Fast intallation
- Bespoke designs
- Excellent lifetimes
- Impact resistant
- Manufactured under high-quality factory conditions
- High-quality materials
- Pre-fired to reduce furnace dry-out time
- Consignment stock
- "Zoned" wear block replacement
Pyrotek's production facility in Cortland, New York, USA, provides engineering and casting services that generate high-quality precast shapes, which are cast under controlled conditions to closely monitor all variables during manufacturing. All shapes are fired to high temperatures to remove moisture and ensure the refractory properties provide a superior furnace lining.
Pyrotek liners are designed per alloy, charge material, temperature, burner design, operator methods and more to combat corrundum growth, mechanical damage, metal penetration, thermal shock, erosion and chemical attack.
Other Related Products
Furnaces will often incorporate other Pyrotek products such as electromagnetic pumps (EMP), mechanical pumps, and LOTUSS scrap melting systems.
- Expertly engineered designs for every customer need
- Vast furnace building experience, creating highest quality liners
- World-class casting facility creates highest quality building materials
- Best construction method and material selection per application
- Reduced turnaround time
TAB Receives Award from Constellium Muscle Shoals | Link | |
1563 Big Block Rebuild Case Study EN | Case Study | English |
Pyrotek TAB Refractory Services Aluminium Insight Article May 2017 EN | Insight Article | English |
Precast Hearth Block Solutions Report | Document | English |