Metal Melting - Foundry
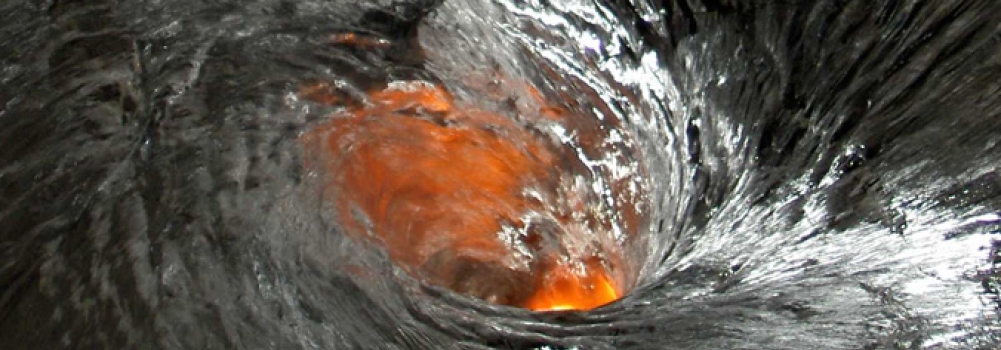
Melting furnaces convert solid aluminium into molten metal and operate at higher energy inputs than holding furnaces. Furnace efficiency varies depending on the type of furnace, controls and scrap charge. The faster the conversion into liquid metal, the less dross or melt loss occurs. Types include reverberatory, which is most widely used, side bay/well reverberatory, dry hearth and stack melter. (Learn about the Pyrotek Tower Melter and Related Metal Handling Equipment.) Melting furnaces need a different refractory lining than a holding furnace due to the higher temperatures and greater mechanical abuse they withstand. They also produce more dross and suffer from corundum and spinel reactions. They must have the melt rate required to feed die casting furnaces to maintain production.
Pyrotek focuses on increasing metal quality and furnace efficiency to improve performance for die casters. Solutions for melting furnaces include circulation pumps, integrated melting systems, precast refractory shapes, flux and flux-injection equipment, furnace tools, engineering services, thermocouples, heated troughs and gaskets and seals.
- Improved energy and furnace efficiency
- Reduced melt loss and increased metal quality
- Less dross
- Higher throughput
- Lower maintenance costs
Additional Information
Pyrotek Tower Melter 1881 | Flyer | English |
1886 Pyrotek Tower Melter and Metal Handling Equipment Brochure | Brochure | English |