Tabletop Refractory
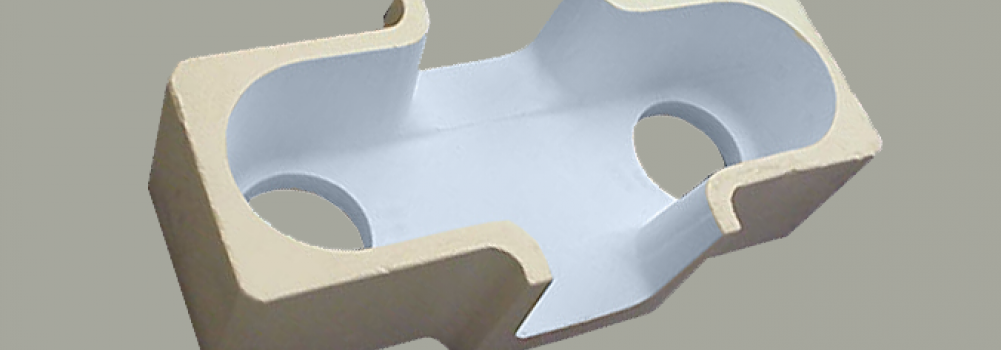
Overview
Pyrotek tabletop refractory includes precast refractory components used to distribute molten metal to mould positions in a vertical direct chill (VDC) billet casting tables. The shape, size and configuration of the components depends on the equipment manufacturer and their specific design preferences. Shapes can be categorized as either trough or feeder components. Trough sections typically include entries, tees, troughs and elbows. Feeder parts are commonly described as cross feeders, half feeders (tee feeders) and end feeders. All feeder shapes contain an aperture in the bottom that delivers metal to the casting and is concentric to the mould. The tabletop refractory assembly are joined using mastic, mastic and ceramic rope, or mastic and ceramic paper gaskets. Typically, a thermal insulation layer is added between the refractory and the casting table weldment in the form of pourable backup insulation refractory or ceramic packing wool. Below the parts, a thin layer of ceramic paper is commonly installed. To deliver repeatable casting performance, tabletop refractory should have a low thermal conductivity to resist heat transfer from molten metal and a high thermal capacity to remain hot between casting cycles while resisting wear, erosion, corrosion, and thermal shock with high hardness, inertness to aluminium and high fracture toughness respectively.
Pyrotek Offerings
Pyrotek offers a variety of tabletop refractory products. Pyrotek's shell-insulated tabletop refractory utilizes a hard-wearing refractory (Pyrocast FS73 AL) that is cast inside a highly insulative refractory (Wollite 45) to increase thermal performance over monolithic shapes. Monolithic tabletop refractory made from Insural 140 refractory delivers very low thermal conductivity and has been the preferred solution for years by many customers. Other ceramic options are available to serve unique customer requirements.
- Improve safety with non-RCF refractory
- Lower thermal gradients across the casting table with insulative design options
- Extend service life with high wearing and thermal shock resistant refractory
- Reduce joint maintenance with low thermal expansion
- Optimize performance with custom shapes
1427 Pyrotek Shell Insulated Tabletop Refractory Armallite 95 EN | Datasheet | English |
1653 Pyrotek Monolithic Tabletop Refractory EN | Datasheet | English |
1651 Vertical Direct Chill Billet Casting Brochure EN | Brochure | English |
991 Refractory Liner Preheat Recommendations Manual ES-MX | Manual | español |