Troughs and Launders
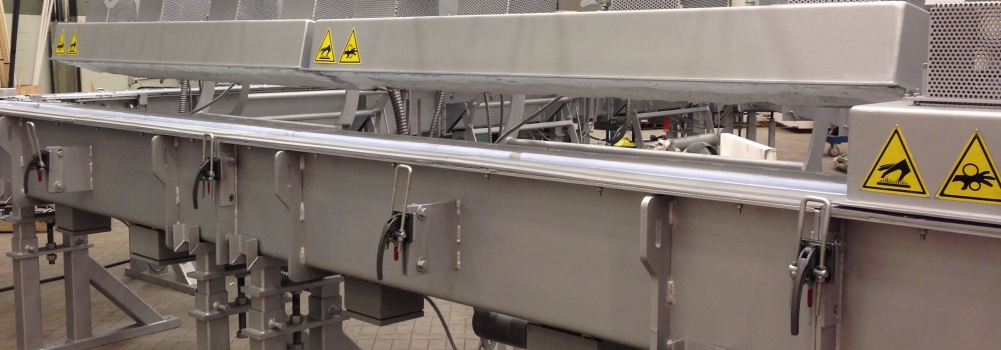
Trough/launder systems carry molten alloys from one location to another through gravity. The systems typically include a hot-face refractory, backup insulation, steelwork, dams and other high-temperature equipment, such as thermocouples and gaskets. They are most often used to transport metal from a melting furnace to a holding furnace, from a holding furnace to a casting station or to carry metal to inline degassing and filtration systems. Effective trough systems help maintain metal temperature and prevent oxide buildup.
In foundries, troughs are typically used in the transport of metals from melting furnaces to holding furnaces. The shape and dimensions of trough systems can vary but usually consist of a refractory hot-face lining and insulation retained within a steel shell. Trough designs must account for metal velocity, metal temperature at the casting station (temperature loss due to distance to casting station), specific alloys to be cast and other variables.
Pyrotek's global network of application experts and engineering centres work with customers to determine the optimal design and materials for their trough systems. Our award-winning heated launder system is designed to maintain molten metal temperature as alloys are transferred, and they are more efficient as heat is conducted rather than radiated, enabling metal temperature to remain uniform, reducing oxides and lowering energy costs. Pyrotek can provide a number of solutions with engineering and manufacturing to design and implement a variety of trough systems. Products include refractory materials, precast shapes, backup insulation, heated trough covers and coatings.
Pyrotek trough refractory benefits:
- High resistance to chemical attack
- Low thermal conductivity
- Excellent mechanical strength
- Thermal shock resistance
- Reduced heat loss
- Better metal quality
- Expert engineering design